The P2 Project has released the latest update on progress to build a class P2 2-8-2 Mikado.
Sir Nigel Gresley designed P2s to haul 600-ton trains on the arduous Edinburgh to Aberdeen route and were the most powerful express passenger locomotives to operate in the UK.
Work is progressing well on the new-build P2 2007 Prince of Wales, and this latest progress report provides an update on producing the cylinder block.
Precision fabricator Howco at Irvine in Scotland has made good progress with the initial machining of parts for the cylinder block and has started to weld them together and assembly of the middle cylinder assembly is progressing well.
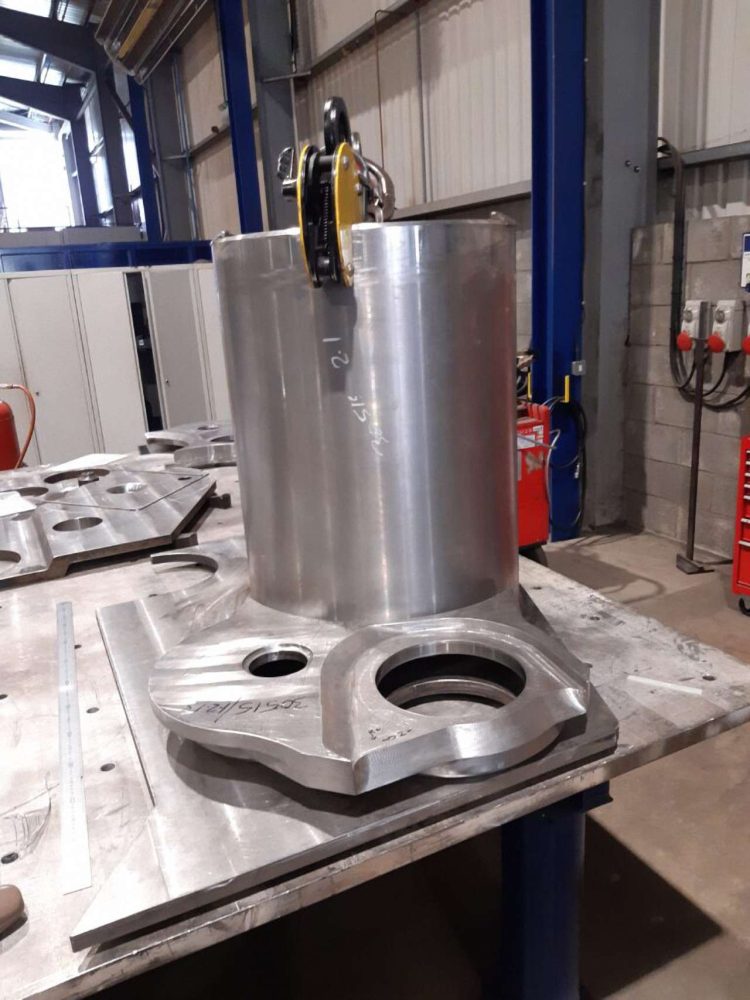
Meanwhile, William Cook Cast Products (WCCP) of Sheffield has completed the casting of the six steam port castings. Their joint faces are now being skimmed so that they can be hydraulically tested to check for leaks.
Although Howco will hydraulically test the entire cylinder block before it is delivered, it is prudent to test the castings separately, as some faces of the steam ports will be inaccessible once they are welded on.
WCCP will have carried out extensive Non-Destructive Testing (NDT) on the castings, but previous experience with bronze castings, even with X-ray inspection, shows that it is not always possible to see minute pinholes which might give rise to leakage, hence the belt and braces approach.
Some detailed machining drawings for the valve ports and cylinders have been produced, drawings of the valve gear and cambox continue to be checked, and a one-third scale model of a cambox has been completed. The material specifications for the critical items, including cams and cam followers, are being refined.
Manufacturing drawings for the cam box and its internal components are largely complete, as are worked-up designs for lubrication of the valve spindles and oil coolers for the camboxes. A one-third scale 3D printed model of the cambox and its internals has also been produced.
I’m a Covenantor and feel ‘part’ of this locomotive’s progress. I’d urge anyone to join – it’s easy – and painless!
The great thing about this project is that you just know it’s going to happen. On time and on budget. Totally professional.