Construction of HS2 has created a great demand for steel, much of which is being produced by CELSA Steel UK and supports hundreds of jobs in South Wales, Yorkshire and Nottinghamshire.
To produce the steel requires scrap metal, and through the UK recycled steel initiative, which is helping HS2 to cut carbon in construction, old car parts, radiators, and shopping trolleys are being given a new lease of life in HS2.
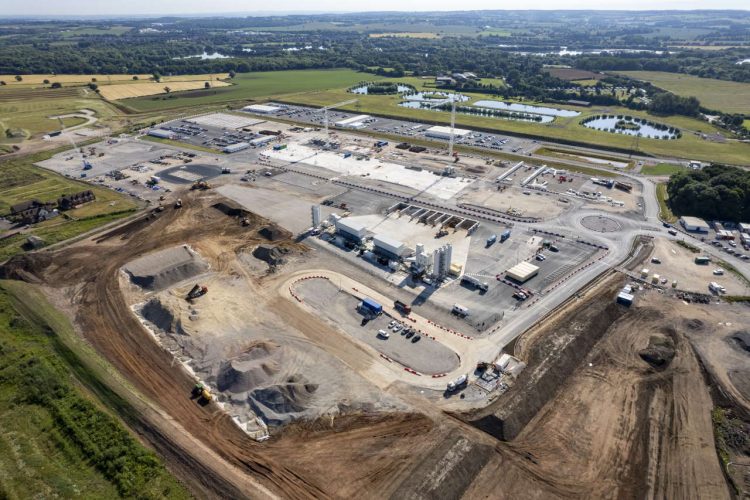
The construction of HS2 is forecast to require over one million tonnes of steel for standard construction materials, 200,000 tonnes for steel rail, switches and slab track, and another 15,000 tonnes for rolling stock.
During the last two years, the UK steel industry has received orders worth over £170m from HS2's construction partners for building the first phase of HS2 between London and the West Midlands.
Much of the steel is being produced by CELSA Steel UK, and over the last two years nearly 20,000 tonnes of steel produced by ROM/CELSA has been used in HS2. Just 100 people work at ROM Ltd.'s Sheffield factory, so a 2,000-tonne order is a ‘big deal'. The company also has around 140,000 tonnes of future orders from just one of HS2's four civil construction partners.
With the current scale of demand, ROM Ltd.'s factory at Brightside in Sheffield facility production of rebar is almost exclusively for HS2. The requirement for another 140,000 tonnes for just one HS2 contractor will account for about 80% of the total output for the next three years.
CELSA Steel UK is the UK's largest manufacturer of steel reinforcement, with 750 staff working at its two sites in Cardiff where recycled scrap metal from the company's scrapyards in Cardiff, Swansea, Rotherham, Bristol and Sunderland is melted in an electric arc furnace to produce billets which are rolled to make reinforcing bar (rebar) for use on HS2 construction sites. Electric arc furnaces produce 80% less carbon emissions than basic oxygen steelmaking.
The rebar produced in Cardiff is transported to ROM GROUP sites in the UK, where it is cut, shaped, and bent to meet the special requirements of HS2's construction partners. firm ROM GROUP is part of the CELSA GROUP,
Up till now, ROMTECH's prefabrication facility at Sutton in Ashfield in Nottinghamshire has taken delivery of 8,000 tonnes of rebar from CELSA's Cardiff mill for welding by a team of 40 specialists to create bespoke prefabricated piling cages each weighing up to ten tonnes and two-metres wide.
These are labelled before being shipped to HS2 construction sites where they are used to strengthen the ground before the construction of bridges, viaducts, and tunnels. Most of CELSA Steel UK's production including scrap steel is transported by rail.
Visiting CELSA Steel UK's Cardiff headquarters, a UK steel provider to HS2, Ruth Todd Chief Commercial Officer at HS2 Ltd said:
“HS2's vast demand for steel over the next 20 years, as we extend Britain's new railway to Manchester and the East Midlands, is a lifeline for this vital UK industry and stimulates future growth potential.
“As I've seen here today, HS2's supplier contracts with CELSA Steel UK are already supporting hundreds of jobs in Cardiff, Yorkshire and Nottinghamshire. Furthermore, the recyclable and retraceable products they supply aligns to our commitment to cut carbon in construction, as we strive to ensure HS2 is one of the most environmentally responsible infrastructure projects ever delivered in the UK.”
Gabriella Nizam, Head of Sustainability and Strategy at CELSA UK said: “HS2 recognise the value of CELSA Steel UK's low carbon steel, and we're delighted our products are supporting the construction of a railway that will deliver zero carbon journeys for millions of people.
“Our steel is produced in an Electric Arc Furnace, with 98% of our raw material being UK-sourced scrap metal. Our commitment to circularity combined with our sustainable production process, establishes us as a leader in environmentally friendly steel production in the UK. While our steel is already low carbon, we are striving to reduce our scope 1 and 2 emissions by 50% by 2030 and becoming a net positive company by 2050.”
Brian Traynor, Managing Director of ROM GROUP said: “HS2 brought some much-needed demand for ROM GROUP during the pandemic, as the orders kept on coming. We've subsequently invested over £ 2 million in new equipment at our Sheffield facility to ensure we can maintain demand and sustain future growth.
“There's a great sense of pride in seeing the steel our workforce has precision cut and bent being used to build the railway, and we hope that continues into the next decade and beyond as HS2 heads north.”
Gareth Stace, Director General of UK Steel, said: “We are proud that UK-made steel is being used to build HS2. With the potential for two decades more orders, HS2's investment in UK recycled steel should be emulated by many other major infrastructure projects.
“By buying UK-made steel, HS2 boosts supply chains and jobs across the country, from Wales to Yorkshire. Choosing domestic steel also means HS2 hits corporate social responsibility obligations and cuts even more carbon emissions by transporting the recycled steel by rail.
“HS2 is core to the fabric of the UK steel industry, which has around 40,000 employees and feeds into an extra 50,000 supply chain and community jobs.”